Mining landscape near Nœux-les-Mines, 8/1949.
La belle France IV.
La belle France III.
La belle France II.
Shafts 2 and 2bis of the Sainte-Henriette colliery in Hénin-Beaumont with coking plant and power station in 1954.
The coking plant was shut down in 1958 and the mine was closed in 1970.
In the background on the left is the notorious Peñarroya lead and zinc smelter.
La belle France I.
Hütte im Sand
Vor 110 Jahren baute Frankreich sein erstes nasses Hüttenwerk an die Küste Flanderns.
Die Geschichte der Usine de Dunes ist heute weitgehend vergessen, obwohl es am Standort in Leffrinckoucke alles gab was ein integriertes Hüttenwerk ausmacht: Kokerei, Hochofen, Stahlwerke und Walzwerke.
1911 durch die aus dem Industrierevier von Saint-Étienne stammende Aciéries et forges de Firminy erbaut sollte das Werk in den Dünen Kokskohlen aus den nahe gelegenen Revieren Nordfrankreichs und Belgiens mit importiertem Hämatiteisenerz aus Schweden kombinieren.
Ein eigenes Hafenbecken am Canal de Furnes verband die Hütte mit dem Hafen von Dünkirchen.
Hochofen und Kokerei wurden während der Weltwirtschaftskrise Anfang der 1930er Jahre stillgelegt (die Kokerei erst 1977 abgerissen). Das SM-Stahlwerk, die Walzstrassen, Schmieden und die Radsatzfertigung blieben erhalten.
1969 beschloss der neue Inhaber (Creusot-Loire) das Werk durch den Bau eines LD-Stahlwerks an die neu gebaute Hütte von Usinor im 16 Kilometer entfernten Dünkirchen anzubinden, ein Liefervertrag für Roheisen an das SM-Stahlwerk bestand bereits. Nach nur 11 Monaten Bauzeit wurde der neue 60 t Konverter am 11. März 1971 erstmals abgestochen.
Die Hütte in Leffrinckoucke betrieb nun drei 100 t SM-Öfen ( 270.000 t/j), einen Elektrolichtbogenofen ( 80.000 t/j) und den neuen LD-Tiegel mit einer Jahreskapazität von 350.000 t.
Auf der Walzwerksseite waren eine Blockstrasse und zwei Stabwalzwerke in Betrieb.
Auch die Radsatzfertigung mit einer 6000 t Räderpresse war noch vorhanden. Die Versorgung mit Roheisen aus Dünkirchen erfolgte durch jeweils zwei 100/150 t Roheisenpfannen. Mehr als 3100 Beschäftigte arbeiteten nun am Standort.
Am 26. März 1978 ersetzte ein neuer 80 t Lectromelt UHP Lichtbogenofen die alten SM-Öfen. Wann das LD-Stahlwerk stillgelegt wurde ist mir leider nicht bekannt, vermutlich aber bei der Übernahme durch Usinor-Sacilor.
Seit den 1980er Jahren kam es dann zu zahlreichen Besitzerwechseln (Ascometall, Lucchini, Severstal, Swiss Steel).
Im Herbst 2017 wurde das Elektrostahlwerk und im April 2020 das letzte Walzwerk in Leffrinckoucke stillgelegt. Auch die verbliebene Wärmebehandlung mit 69 Beschäftigten soll verlagert werden.
Borsig
Während im Bergbausektor inzwischen an viele, selbst kleinere, Schachtanlagen mit eigenen Monografien erinnert wird verschwinden ganze Stahlstandorte schon wenige Jahre nach ihrer Schließung im Nebel des Vergessens.
Ein typisches Beispiel sind die Borsigwerke in Berlin-Tegel die heute den meisten bestenfalls noch als Maschinenbauunternehmen in Erinnerung sind.
In den 1950er Jahren unterhielt die Borsig AG hier noch Siemens-Martin Öfen, Walz- und Schmiedewerke, ein Röhrenwerk und eine Graugiesserei.
1968 begann in Tegel der Abschied von der Stahlsparte, Borsig verkaufte seine 1954 gebaute Mittelbandstrasse (400 mm, Kapazität 288.000 t/j) an die August Thyssen Hütte, dort lief sie fortan unter dem Namen Thyssen Bandstahl Berlin GmbH.
Das Vormaterial, Brammen, kam aus Duisburg. Später wurden auch Lohnwalzungen für das Eisenhüttenkombinat Ost in der DDR durchgeführt.
1992 legte die Thyssen Stahl AG ihr Werk in Berlin still.
Bei der Stahlerzeugung ging Borsig 1970 eine Kooperation mit dem Betonstahlhersteller Walzwerke Becker aus Euskirchen ein. Gemeinsam baute man ein Elektrostahlwerk (30 t Lichtbogenofen, 100.000 t/j) und eine Strangussanlage für Knüppel im wesentlichen zur Versorgung der 14-gerüstigen Stabstahlstrasse in Euskirchen.
Alle Anlagen wurden von der DEMAG in Duisburg geliefert.
Offenbar hat die Walzwerk Becker KG (Wabec) das Stahlwerk dann ab 1981 in Eigenregie weitergeführt.
1984 lieferte die Mannesmann-DEMAG AG einen neuen Lichtbogenofen mit konzentrischem Bodenabstich (50 t). Der Standort lief jetzt unter den Namen Berliner Stahlwerk KG Gerd Becker und Walzwerk Becker-Berlin Strangguss KG.
1988 wurden diese Firmen insolvent und der türkische Staatskonzern Metek Teknik aus Izmir übernahm das Werk. Trotz anders lautender Versprechungen blieben Investitionen aus und 1992 wurde die Stahlproduktion in Berlin durch Metek endgültig beendet.
In der aktuellen Ausstellung “Wir sind von hier. Türkisch-deutsches Leben 1990“ mit Fotografien von Ergun Çağatay auf der Zeche Zollverein sind drei Bilder aus dem Stahlwerk Berlin zu sehen. Ansonsten ist die Quellenlage zum Stahlstandort Berlin-Tegel sehr überschaubar.
Kühnle, Kopp & Kausch
Einer der vielen interessanten Zulieferer der Stahlindustrie war die 1899 gegründete Firma Kühnle, Kopp & Kausch aus Frankenthal in der Pfalz.
Vielen sicher bekannt durch ihre Turbolader für die Automobilindustrie (KKK).
Nach div. Inhaberwechseln (Borg-Warner, MTU, Daimler-Benz, Siemens) stellt heute die Firma Howden Turbo aus Schottland weiterhin Dampfturbinen und Verdichter in Frankenthal her.
Hier eine Werbung für den französischsprachigen Markt mit zwei Gebläsen einer belgischen Sinteranlage.
Train de 380
Among the most frequently photographed relics of the wallonian steel industry are the, empty, halls of the former light sections rolling mill (Train de 380) of the Soc. Hainaut-Sambre in Charleroi-Montignies.
Nevertheless, there are hardly any pictures of the working plant to be seen. Furthermore, many explanations about the site are wrong or inaccurate.
Therefore here are some additions.
The rolling mill was built by J. Banning AG of Hamm, Germany and installed in 1968/69. Commissioning took place on 29.9.1969.
The rolling mill consisted of a walking beam furnace, four 2-high roughing stands, 2 x 2 intermediate stands, and four finishing stands (two of these in vertical arrangement).
Downstream, there was a rake-type cooling bed (65 m) and four shears.
The plant was shut down after just 11 years on 8.3.1980.
The whereabouts of the rolling mill are unfortunately unknown to me, but a resale seems likely.
Bruckhausen
Da es bei thyssenkrupp Steel nordwestlich des Oxygenstahlwerks in Bruckhausen z.Z. zu nicht unerheblichen Abrissarbeiten kommt hier mal eine grobe Übersicht über die ehem. dort vorhandenen Anlagen.
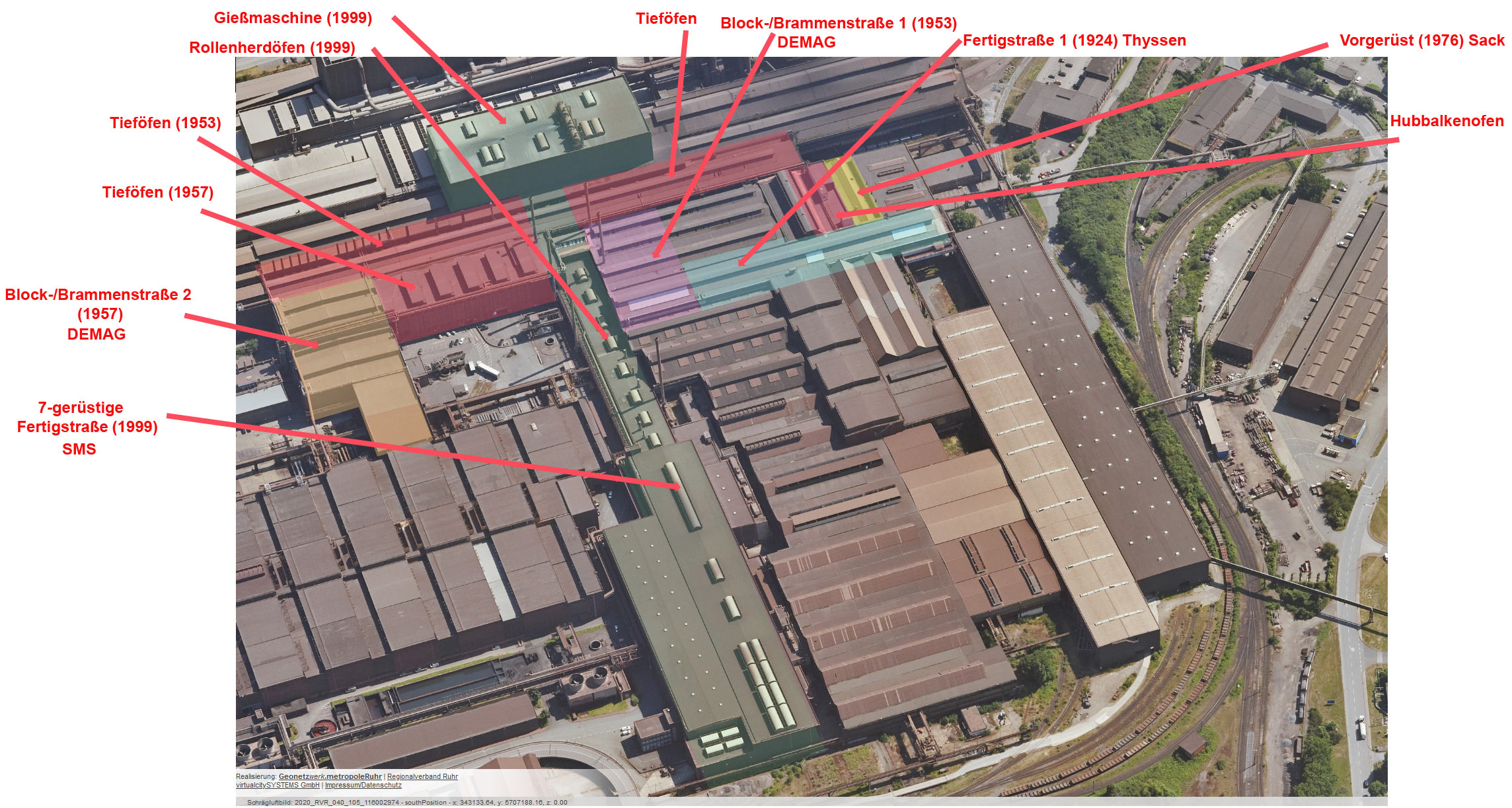
© RVR, 2020, dl-de/by-2-0