Da es bei thyssenkrupp Steel nordwestlich des Oxygenstahlwerks in Bruckhausen z.Z. zu nicht unerheblichen Abrissarbeiten kommt hier mal eine grobe Übersicht über die ehem. dort vorhandenen Anlagen.
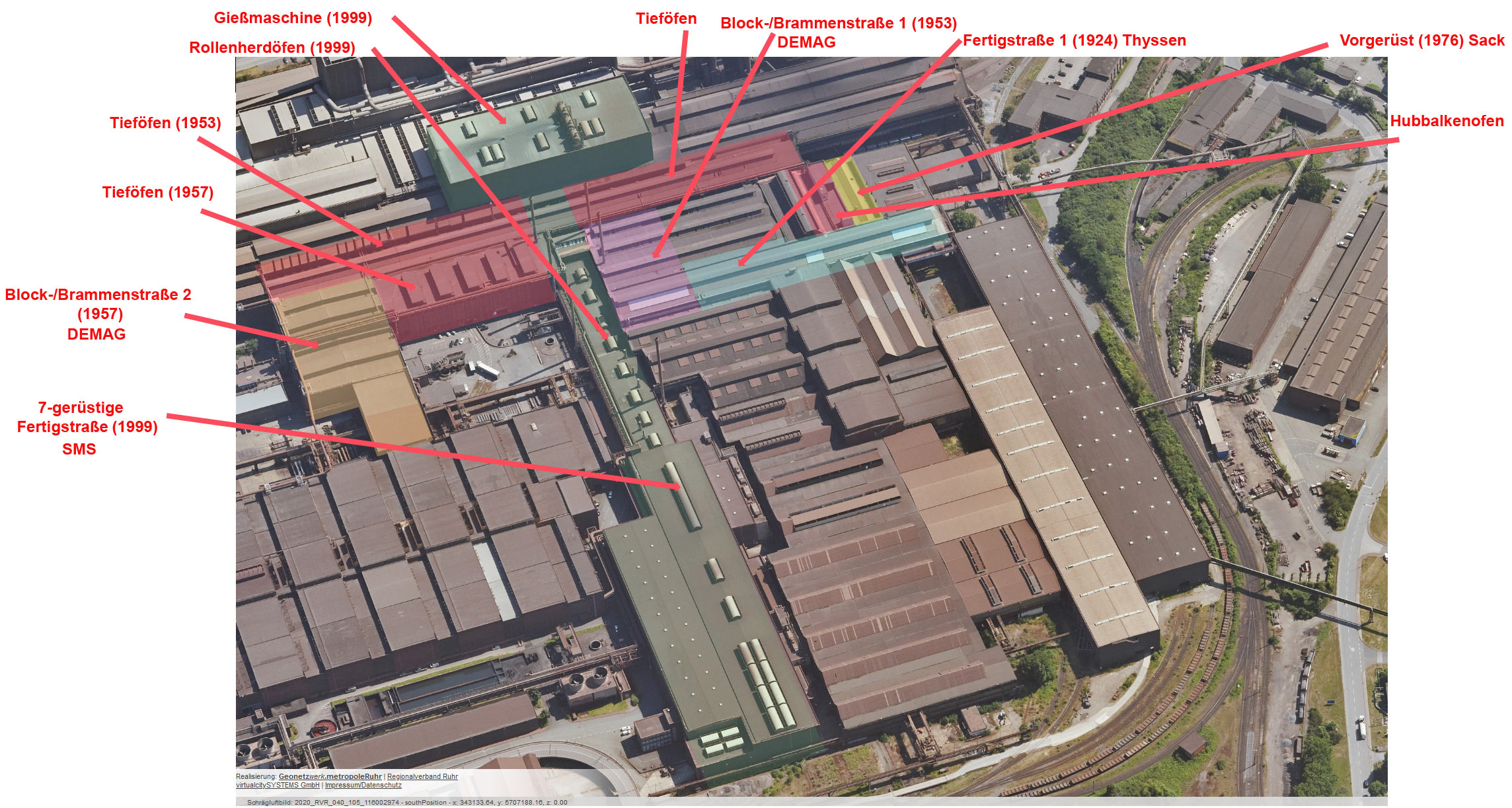
© RVR, 2020, dl-de/by-2-0
Da es bei thyssenkrupp Steel nordwestlich des Oxygenstahlwerks in Bruckhausen z.Z. zu nicht unerheblichen Abrissarbeiten kommt hier mal eine grobe Übersicht über die ehem. dort vorhandenen Anlagen.
© RVR, 2020, dl-de/by-2-0
Da sich auf Zollverein zurzeit einiges Interessantes tut zur Abwechslung mal etwas Bergbaukram.
Auf der Schachtanlage Zollverein 12/1/2/8 existiert seit ihrer Stilllegung eine Anlage zur Hebung von Grubenwässern. Genauer gesagt handelt es sich eigentlich um zwei Wasserhaltungen; die Ende der 1980er Jahre auf -948 mNN eingerichtete Wasserhaltung für die Wasserprovinz Zollverein-Süd1 und die seit 2008 auf -963 mNN arbeitende Wasserhaltung der Provinz Zollverein Stinnesdamm/Emschermulde².
Beide Wasserhaltungen teilen sich eine Pumpenkammer welche die Grubenwässer über den Schacht Zollverein 2 getrennt zur Einleitung in die Emscher abführt.
Im Rahmen des mit den Behörden vereinbarten Grubenwasseranstiegs auf circa. -600 mNN wird die Wasserhaltung der RAG im zentralen Ruhrgebiet nun komplett neu strukturiert (Karte).
Die Wasserhaltungen, Zollverein, Carolinenglück, Amalie und Auguste Viktoria wurden oder werden zeitnah (2021) eingestellt, die betreffenden Schächte verfüllt und mit Hüllrohren zu potentiellen Brunnenwasserhaltungen umgebaut.
Nach einer Anstauphase von mehreren Jahren sollen alle Grubenwässer der stillgelegten Wasserprovinzen in die Wasserprovinz Zollverein/Emschermulde übertreten³.
Ab 2026 soll das Niveau in der Provinz Zollverein/Emschermulde auf -726 mNN angestiegen sein und das Wasser dann im Bereich der ehem. Zeche Möller-Rheinbaben unter Bottrop in das Grubengebäude der Zeche Prosper-Haniel übertreten.
Von dort würde das es dann über den Schacht Hünxe zur 5. Sohle des Bergwerks Lohberg in Dinslaken fließen und in den Rhein abgepumpt werden.
Faktisch würde es also im zentralen Ruhrgebiet dann nur noch eine Wasserprovinz geben (Lohberg).
Das aus nicht verfüllten Abbaubereichen, Strecken, Schächten, Poren und Klüften bestehende Restholraumvolumen allein in dieser Provinz wird auf über 500 Mio. m³ geschätzt was dem einhundertneunzigfachen Volumen der Cheops-Pyramide entspricht.
Die Wassergängigkeit zwischen den verschiedenen Wasserprovinzen soll durch (z.T. neu aufgefahrene) Strecken, Bohrlöcher oder ehem. Abbauannäherungen der Zechen gewährleistet sein.
Problematisch erscheint die Übertrittsstelle Emschermulde-Haniel. Hier würde das gesamte Grubenwasser der stillgelegten Wasserprovinzen um Zollverein in die Provinz Haniel übertreten (circa 22 Mio. m³/J).
Mit einer 2200 m langen Erkundungsstrecke (letzte Streckenauffahrung im dt. Steinkohlenbergbau) ist daher 2015 von der Schachtanlage Haniel 2 aus dieser Bereich angefahren worden. Dabei wurde festgestellt, daß die aus den 1950er Jahren stammende, als Übertrittsstelle vorgesehene, ehem. Richtstrecke der Zeche Möller-Rheinbaben verbrochen ist.
Ob eine Ableitung der Grubenwässer nach Westen über die neue Erkundungsstrecke/Grubenwasserkanal in Gänze möglich seien wird ist also offen.
Bei einem teilweisen Versagen der Wasserwegigkeit sollen daher ab 2030 über den Schacht Zollverein 12 wieder bis zu 5,8 Mio. m³ pro Jahr gehoben werden.
Dafür belässt man in der anstehenden Schachtverfüllung zwei Hüllrohre zum Einbringen von Tauchpumpen. Das abgepumpte Grubenwasser soll anschließend übertägig zum ehem. Förderberg der Schachtanlage Prosper-Haniel fließen. Dazu würden bis zum RH-Kanal die vorhandenen Grubenwasserleitungen genutzt. Vom Bereich Schurenbachhalde bis zur Schachtanlage Prosper-Haniel würde eine neue Rohrtrasse entlang des RH-Kanals notwendig.
Um das Zollvereingrubenwasser durch den 3700 m langen Förderberg (davon 1170 m verfüllt) wieder nach Untertage einleiten zu können wurden dort kürzlich zwei Stränge aus insgesamt 2860 Betonröhren eingebaut.
Bei -626 mNN würde dieses Wasser dann dem Grubenwasserstrom Richtung Lohberg zugeführt und dort zum zweiten Mal gehoben.
Für den, unwahrscheinlichen, Fall eines Totalversagens der Überleitung im Grubenfeld Möller-Rheinbaben müßte auch der Schacht Zollverein 2 mit Tauchpumpen ausgestattet werden und zur Wasserhebung herangezogen werden. Da sich wg. schädlicher Ausfällungen die bariumhaltigen Grubenwässer aus der Wasserprovinz Zollverein-Emschermulde nicht mit den sulfathaltigen aus der Provinz Zollverein-Süd mischen sollen wird auf der 14. Zollvereinsohle ein Damm mit einem regelbaren Durchlass eingebaut der die Grubenwässer im Bedarfsfall trennen könnte.
Abgesehen von der hier beschriebenen Wasserhaltung im zentralen Ruhrgebiet wird es weiterhin die Wasserhaltungen Haus Aden (Einleitung Lippe), Robert Müser, Friedlicher Nachbar, Heinrich (Einleitung Ruhr) und Walsum (Einleitung Rhein) geben.
Die Grubenwässer aus der Wasserhaltung Concordia in Oberhausen werden zukünftig in die Wasserprovinz Walsum übertreten und dort abgepumpt.
Fernziel ist es alle Wasserhaltungen auf Brunnenbetrieb umzustellen auch um zukünftig kein Personal für den Untertagebetrieb mehr vorhalten zu müssen (z.B. Grubenwehr).
Das heißt natürlich auch, daß es in Kürze keinen Zugang zum ehem. Steinkohlentiefbau des Ruhrgebiets mehr geben wird.
Wer sich gerne näher mit dem Thema Grubenwasserkonzept befassen möchte:
Machbarkeitsstudie 1
Machbarkeitsstudie 2
Einleitung Förderberg Prosper
1 Grubenfelder: Zollverein V/VI, Zollverein-SW, Dahlbusch/Holland, Bonifacius, Katharina, Kg. Elisabeth, Vict. Mathias.
2 Grubenfelder: Zollverein III, Emil-Fritz, Prosper alt, Möller-Rheinbaben, Math. Stinnes, Wilh. Victoria, Nordstern, Graf Moltke, Hugo, Bismarck, Ewald, Schlägel & Eisen, Pluto, Consolidation, Recklinghausen, Blumenthal, König Ludwig, Ewald Fort., An der Haard, Emscher Lippe, Waltrop.
3 Carolinenglück (2022), Amalie (2022), AV > 2030.
Der Mythos der Stahlstadt Essen hat Dank der Fried. Krupp AG den 2. Weltkrieg überdauert.
Man sprach immer noch von der Essener Gußstahlfabrik.
Tatsächlich gab es aber nach 1945 keine nennenswerte Stahlproduktion mehr in der Stadt.
Vor dem Krieg (1936) hatte Krupp in Essen noch 261.000 t Roheisen und 625.000 t Rohstahl produziert. Nach der Stilllegung und Demontage des Hochofenwerks in Borbeck und der drei Siemens-Martin Stahlwerke produzierte Krupp 1960 nur noch in jeweils einem Lichtbogenofen und einem Kupolofen (24) Stahl und Eisen für den Eigenbedarf der Schmiede (13) und der Eisengießerei (24). Ansonsten handelte es sich bei Krupp in Essen nun um ein Sammelsurium aus Leichtmachinen-, Schwermaschinen- und Anlagenbau, Fahrzeugbau und Dienstleistern.
1960 wurden auch große Bereiche der ehem. Gußstahlfabrik durch Fremdfirmen genutzt oder waren verkauft worden (z.B. die Landmaschinenfertigung an der Hans-Böcklerstr.).
Das Luftbild zeigt den Zustand in den frühen 1960er Jahren.
Die Massenstahlerzeugung war zu diesem Zeitpunkt schon nach Rheinhausen und zum neu erworbenen Bochumer Verein verlagert worden.
© RVR, 1969, dl-de/by-2-0
1 Widia
2 Baubetriebe
3 Bürohaus Westbahnhof
4 Lagerhaus Chemiebau
5 Unfallambulanz
6 Grafische Anstalt
7 Mechanische Werkstatt, Labor
8 Gas- und Wasserwerke
9 Eisen u. Stahlhandel, Krupp-Indien Handelsgesellschaft
10 Sauerstoff- Wasserstoff- Druckluftversorgung, Zurichterei
11 Essener Schweißelektrodenwerk
12 Krupp Dolberg
13 Press- und Hammerwerk
14 Krupp Ardelt
15 Konzernleitung, Turmhaus
16 Bürogebäude 2
17 Lehrwerkstatt
18 Motoren- und Kraftwagenfabriken
19 Motoren- und Kraftwagenfabriken
20 Bergwerk Helene-Amalie
21 Leichtmaschinenbau, Apparatebau
22 Pressenbau, Getriebebau
23 Lokomotivbau, Dieselmotorenbau
24 Gießerei, LD-Versuchsstahlwerk
Mit der gestrigen Mittagsschicht hat thyssenkrupp Steel die Produktion von Grobblechen eingestellt.
Das Grobblechwalzwerk in Duisburg-Hüttenheim wurde 1963 durch die Mannesmann AG zur Versorgung des benachbarten Großrohrwerks (Stilllegung 1978) mit Blechen erbaut.
1970 übernahm die August Thyssen Hütte im Tausch mit ihren Rohrwerken die Flachstahlsparte von Mannesmann. 1978 wurde das neue 3,9 Meter Quartogerüst durch die Sack Maschinenbau GmbH installiert.
Die von Krupp hergestellten Roheisenpfannen wurden auch von anderen Stahlherstellern genutzt, z.B. von Klöckner auf der Route Georgsmarienhütte-Bremen oder später (mit geänderten Wagennummern) von Thyssen zwischen Oberhausen und Hattingen.
Einer der letzten noch existierenden Wagen wurde im Januar von Duisburg zu einer Spedition in Hattingen überführt. Er soll später im LWL-Industriemuseum Henrichshütte ausgestellt werden.
Danke für die Infos und die Bilder an Christoph Oboth.
Ende Juni 1968 wurde der letzte Bochumer Hochofen, der Ofen 1, stillgelegt, fortan mussten die Bochumer Stahlwerke der Fried. Krupp Hüttenwerke von Rheinhausen aus mit Roheisen versorgt werden.
Am 16.2.1968 begann der am längsten währende Roheisenverbund über das DB-Netz in der Geschichte des Ruhrgebiets.
Roheisenzug b. Essen-Frohnhausen © Eisenbahnstiftung, H.D.Kremer
Der Roheisenbedarf des LD-Stahlwerks Bo-Höntrop lag 1967 bei 60.000 t/m, die Siemens-Martin Stahlwerke benötigten, bei 30%-Einsatz, etwa 15.000 t/m.
Diese Mengen wurden nun in, von Krupp speziell für den DB-Einsatz entwickelten, Roheisenpfannen angeliefert.
Durch Ein-Konverterbetrieb im LD-Stahlwerk und Stilllegung von SM-Öfen konnte der Verbrauch zwar gedrosselt werden, trotzdem rollten schon innerhalb der ersten beiden Jahre 1 Mio. Tonnen Roheisen nach Bochum.
Täglich fuhren zunächst zwischen 12-14 Roheisenzüge.
Die für den Transport genutzten Torpedopfannen unterschieden sich deutlich von den werksinternen Fahrzeugen.
Um die Achslast auf den DB-Strecken zu minimieren waren sie sehr lang (34m) und schmal und hatten eine relativ geringe Zuladung von nur 160 t Roheisen. Das Gesamtgewicht betrug 374 t und verteilte sich auf 18 Achsen.
Das 1400 Grad heiße Eisen kühlte bei der circa 70 Min. dauernden Fahrt um etwa 6 °C ab.
Um die von der DB geforderte max. Außentemperatur von 80 °C einzuhalten verwendete Krupp gelochte Distanzbleche an der Außenseite der Behälter.
Die Streckenführung lief über Mühlheim und dann auf der Trasse der ehem. Rheinischen Bahn über Essen-Nord, Gelsenkirchen-Wattenscheid nach Bochum-Nord.
Die zunächst eingesetzten Dampfloks konnten nach der Elektrifizierung der Rheinischen Bahn durch leistungsstärkere E-Loks ersetzt werden, was vor allem auf der Steigungsstrecke aus dem Ruhrtal bei Mülheim von Vorteil war.
Häufig gemeinsam mit den Torpedopfannen transportierte Krupp 30.000-40.000 t/m heiße Stahlblöcke in speziellen Thermowagen zur Versorgung des Warmbreitbandwerks nach Bochum.
1982 wurde das letzte Siemens-Martin Stahlwerk in Bochum stillgelegt und die Produktion durch den neuen UHP-Lichtbogenofen übernommen.
Die Roheisentransporte konnten nach 14 Jahren eingestellt werden.
wie sie heute nicht mehr zu sehen ist.
Die beiden, recht seltenen, Ansichten zeigen die ehem. auf der Nordseite der Ofenbatterien verlaufende Bandbrücke zur Beschickung der Gasgeneratoranlage (Bild 1 links im Hintergrund) mit Kleinkoks und Koksgrus aus der Sieberei (rechts).
Die Eigenerzeugung von Schwachgas (Generatorgas) aus Koks ermöglichte es der Kokerei, in Ermangelung eines Gasverbundes mit einem benachbarten Hüttenwerk, bis zu 800.000 m³ ihres Kokereigases (Starkgas) am Tag zusätzlich in das lukrative Ferngasnetz abzugeben.
Mit der Verdrängung des Stadtgases durch höherenergetisches und billigeres Erdgas in den 1960er Jahren wurde dieser Weg zunehmend unattraktiv.
Nach der Erweiterung der Kokerei um die beiden Großbatterien 0 und 9 (im Bild noch nicht zu sehen) in 1972 wurde daher die Schwachgaserzeugung eingestellt und die Generatoranlage nebst Bandbrücke verschwanden.
Fortan erzeugten die beiden neuen Batterien Gas für den Eigenverbrauch aller Koksöfen und die alten Batterien 1-8 gaben ihr Gas weiter in das Netz ab.
Um den unterschiedlichen Ansprüchen der Abnehmer an den Reinheitsgrad des Gases zu entsprechen wurde die Gasreinigung getrennt.
Die Hüttenwerk Oberhausen AG (HOAG) war 1965 ein integriertes Hüttenwerk mit einer aus heutiger Sicht erstaunlichen Fertigungsbreite.
Allein am Standort Oberhausen waren 12 Walzstrassen in Betrieb.
Neben Massenprodukten aus Thomasstahl wurden auch Qualitätsstähle für Schmiedestücke, Radsätze und Bleche aller Art erzeugt.
Durch die zwangsweise Ausgliederung der GHH in Sterkrade und dem damit verbundenen Wegfall der Maschinen-, Stahl- und Anlagenbauaktivitäten in 1953 hatte die Fertigungstiefe allerdings deutlich gelitten.
Im September 1964 waren auf der Hütte 13.565 Arbeiter und Angestellte beschäftigt.
In den 1950er Jahren versuchte die HOAG mit einem groß angelegten Investitionsprogramm Anschluss an die technische Entwicklung in der Stahlindustrie zu halten.
In diese Dekade entstanden der neue Großhochofen A (als dritter Großhochofen im Ruhrgebiet), die Blockbrammenstraße, die kontinuierliche Halbzeugstraße, die Feineisenstraße und 1957 schließlich die von Schloemann gefertigte 3,4 Meter Quarto-Grobblechstraße.
1960 waren noch das Siemens-Martin Stahlwerk 2b mit seinen beiden 250 t Öfen und 1963 die kont. Drahtstrasse 2 in Betrieb genommen worden.
Nach wie vor besaß die HOAG aber Mitte der 1960er Jahre noch kein modernes Blasstahlwerk. Versuche mit zwei Graef-Rotoren zur Erzeugung hochwertiger Stähle wurden 1961 eingestellt und spätere Pläne für den Neubau eines kompakten LD-Stahlwerk an Stelle des SM-Stahlwerks 2a nie realisiert.
Auch die ungünstige Lage des Werkes zum Rhein als Haupttransportweg für Importerze (1965 kamen 94,5 % der bei der HOAG verhütteten Erze aus dem Ausland) wurde zunehmend zur Belastung.
Der Bau eines zweiten Großhochofens (B) wurde daher zurückgestellt und eine Kapazitätserhöhung durch Modernisierung der Öfen 3,8 und 9 erzielt.
1966 wurden das Siemens-Martin Stahlwerk 1 und die alte Drahtstrasse 1 stillgelegt.
1968 übernahm die August Thyssen Hütte AG die Aktienmehrheit an der HOAG.
Da bei der ATH ein zweites Oxygenstahlwerk (Bruckhausen) schon im Bau war beschloss man das Thomasstahlwerk in Oberhausen stillzulegen und die dadurch freiwerdende Roheisenmenge (60 % der HOAG-Erzeugung) fortan in flüssigem Zustand nach Duisburg zu liefern.
Eine schwarze Fahne am Hochofen 9 verkündete am 28.2.1969 das Ende der Eisenhütte 1. Der Ofen 8, der letzte noch produzierende am ältesten aktiven Hochofenstandort des Ruhrgebiets wurde ausgeblasen. Nun wurde nur noch auf der Eisenhütte 2 mit zwei Öfen Roheisen erzeugt.
Im Zuge der ATH-Übernahme kam es in Oberhausen noch zu zahlreichen weiteren Anlagenschließungen:
1968: Schwere Profilstraße (750er Straße), Thomasstahlwerk und Blockstraße.
1969: Pfannensinteranlage.
1970: Schlackenmühle, Sauerstoffanlage und Duogrobblechstraße.
1971: Mittelblechstraße, kont. Halbzeug- und 850er Vorblockstraße.
Im gleichen Jahr fusionierte die ATH ihre Töchter HOAG und Niederrheinische Hütte AG
zur Thyssen Niederrhein AG mit Sitz in Oberhausen (Umsatz 71/72: 1,37 Mrd. DM.).
Nördlich von Tor 3, an der Essenerstraße, war zwischen 1970 und 1977 eine Großversuchsanlage (Purofer) zur Direktreduktion von Eisenpellets zu Eisenschwamm in Betrieb. Die Tagesleistung lag bei 500 t.
1972 wurde auf dem Gelände der ehem. Zeche Oberhausen in der Halle der stillgelegten
Kaltbandscherenlinie ein neues Presswerk mit einer 2500 t Kümpelpresse in Betrieb genommen. Das alte Presswerk im Walzwerk Oberhausen wurde geschlossen.
Im gleichen Jahr stellte man den Hochofen A neu zu.
Im September 1972 waren 8965 Arbeiter und Angestellte auf der Hütte beschäftigt.
Der Hochofen 3 wurde im Februar 1975 stillgelegt, die Hütte produzierte nun mit nur noch einem Hochofen.
1977 verkündete der Vorstandsvorsitzende der Thyssen AG Dieter Späthmann “Das Siemens-Martin Stahlwerk unserer Tochtergesellschaft Thyssen Niederrhein in Oberhausen ist zu einer Quelle untragbarer Verluste geworden”. Noch im gleichen Jahr wurde ein Sanierungsprogramm beschlossen das die Weichen für die Flüssigphase am Standort Oberhausen stellte.
Hochofen und SM-Stahlwerk sollten durch ein modernes Elektrostahlwerk mit Knüppel-Stranggießanlage ersetzt werden. Vormaterial für die Grobblechstrasse sollte fortan aus Duisburg kommen, sodass auch die Blockbrammenstraße in Oberhausen 1977 stillgelegt werden konnte.
Baubeginn der 140 Mio. DM Investition war 1979.
In die Halle des im Juli 1977 stillgesetzten SM Stahlwerks 2b wurden zwei 120 t Elektrolichtbogenöfen eingebaut und am 27.2.1980 in Betrieb genommen.
Das SM Stahlwerk 2a lief während der Bauzeit weiter. Erst im März 1980 endete die Siemens-Martin Stahlproduktion in Oberhausen.
Schon im August 1979 war die Roheisenerzeugung in Oberhausen ausgelaufen. Der Hochofen A wurde stillgelegt und im Sommer 1980 gesprengt. Die 4000 t Stahlschrott konnten im neuen Elektrostahlwerk wieder eingeschmolzen werden.
Im Mai 1983 waren bei TN in Oberhausen noch 6010 Arbeiter und Angestellte beschäftigt.
Ende 1983 stellte die Thyssen Stahl AG (ehem. ATH) ein Strukturkonzept zur Kostenreduzierung in seinen Werken vor. Insgesamt sollten 8000 Arbeitsplätze abgebaut werden. Thyssen begann seine Grobblechaktivitäten von Oberhausen und Hattingen auf die 1970 von Mannesmann übernommene und 1978 modernisierte Straße in Duisburg-Hüttenheim zu verlagern.
Für Oberhausen bedeutete das die Schließung eines weiteren Kernaggregats; der 3,4 m Grobblechstrasse. Auch das Presswerk wurde 1984 stillgelegt. Der Ofen 1 im Elektrostahlwerk wurde auf Bodenabstich umgebaut, während des Umbaus nahm man den Ofen 2 wieder in Betrieb.
1986 stellte die Thyssen Stahl AG ein Profilstahlkonzept vor, daraufhin beendete die Feinstahlstraße in Oberhausen ihre Produktion.
Im gleichen Jahr verlor die Thyssen Niederrhein AG endgültig ihre Selbstständigkeit und wurde zur Betriebsabteilung der Thyssen Stahl AG.
1987 brachte das Ende für das 550er Mittelprofilwalzwerk.
Nun waren nur noch das Elektrostahlwerk und die Drahtstrasse 2 in Betrieb.
Bis Ende 1988 war die Belegschaft in Oberhausen auf etwa 2000 heruntergefahren worden.
1990 stellte auch das letzte Oberhausener Walzwerk, die Drahtstraße 2, die Produktion ein die Drahterzeugung wurde nach Duisburg-Hochfeld verlagert.
Nun verlieb nur noch die 1994 ausgegliederte Stahlwerk Oberhausen GmbH mit circa 500 Beschäftigten. Eine 1992 geplante Kooperation mit dem italienischen Stahlproduzenten Beltrame und der gemeinsam geplante Bau eines Stabstahlwalzwerks scheiterten auch an den Bauplänen für ein Einkaufszentrum auf der HOAG-Brache.
Am 19.12.1997 legte Thyssen das Elektrostahlwerk still, 2006 wurde es gesprengt.
Dank an das thyssenkrupp Konzernarchiv, das Stadtarchiv Oberhausen und das Rheinisch-Westfälische Wirtschaftsarchiv in Köln für die Unterstützung bei der Erstellung dieser Karte.
1959 gab es in der Bundesrepublik Deutschland noch 156 Hochöfen an 38 Standorten. Alle Standorte und alle Hochöfen sollen in dieser Serie im Kurzportrait vorgestellt werden.
Vier Hochöfen waren 1959 im heutigen Landschaftspark Nord vorhanden.
Der 1955 errichtete Hochofen 1, die beiden Öfen 3&4 die noch aus der Originalsubstanz von 1904/06 stammten, sie wurden noch über Senkrechtaufzüge und Hängebahnen begichtet, und der 1952 erbaute Hochofen 5. Der Hochofen 2 befand sich 1959 im Abbruch und ist erst 1963 wieder angeblasen worden.
Die Hochöfen 3&4 wurden Ende der 1960er Jahre stillgelegt und abgerissen und der Ofen 5 1973 unter Erhalt von Schrägaufzug und Windenhaus neu erbaut.
Anfang der 1980er Jahre wurde dann vor dem Hintergrund der weltweiten Stahlkrise die Roheisenproduktion im Werk Hüttenbetrieb (inzwischen wieder zu Thyssen gehörig) heruntergefahren und der Hochofen 1 1982 und der Ofen 2 1984 stillgelegt.
Der Hochofen 5 der nun nur noch Manganeisen erzeugte folgte 1985.
Seit 1994 gehören die drei Hochöfen zum Landschaftspark Duisburg-Nord.
Hochöfen Phoenix-Rheinrohr, Werk Hüttenbetrieb 1959.
Hochofen 1: Gestelldurchmesser 5,2 m.
Hochofen 3: Gestelldurchmesser 4,5 m.
Hochofen 4: Gestelldurchmesser 5,2 m.
Hochofen 5: Gestelldurchmesser 5,2 m.
Eine weitere Walzstrasse die sich an der Ruhr z.Z. im Abriss befindet ist die im März 1968 in Betrieb genommene Drahtstrasse IV der ehem. Niederrheinischen Hütte in Duisburg-Hochfeld.
Das 4-adrige vollkontinuierliche Walzwerk ersetzte damals die älteren Strassen I und II in Hochfeld.
Sie bestand aus einer 7-gerüstigen Vorstrasse, einer 8-gerüstigen Zwischenstaffel und vier Fertigblöcken.
2013 übernahm die neue Drahtstrasse von ArcelorMittal in Duisburg die Produktion aus Hochfeld.
Die alte Strasse IV wurde danach meines Wissens nach Nordafrika verkauft.