und Verpuppenstubung von Industrieanlagen schreitet auch in China erfolgreich voran.
Funktionale Zusammenhänge spielen, wie bei uns, beim Erhalt nur eine sekundäre Rolle. Und so wandert der letzte Antikhochofen mal eben auf den Parkplatz vors Werkstor.
Rolltreppen dürfen natürlich auch nicht fehlen.
Author Archives: Uwe Niggemeier
Wasserhaltung Zollverein
Da sich auf Zollverein zurzeit einiges Interessantes tut zur Abwechslung mal etwas Bergbaukram.
Auf der Schachtanlage Zollverein 12/1/2/8 existiert seit ihrer Stilllegung eine Anlage zur Hebung von Grubenwässern. Genauer gesagt handelt es sich eigentlich um zwei Wasserhaltungen; die Ende der 1980er Jahre auf -948 mNN eingerichtete Wasserhaltung für die Wasserprovinz Zollverein-Süd1 und die seit 2008 auf -963 mNN arbeitende Wasserhaltung der Provinz Zollverein Stinnesdamm/Emschermulde².
Beide Wasserhaltungen teilen sich eine Pumpenkammer welche die Grubenwässer über den Schacht Zollverein 2 getrennt zur Einleitung in die Emscher abführt.
Im Rahmen des mit den Behörden vereinbarten Grubenwasseranstiegs auf circa. -600 mNN wird die Wasserhaltung der RAG im zentralen Ruhrgebiet nun komplett neu strukturiert (Karte).
Die Wasserhaltungen, Zollverein, Carolinenglück, Amalie und Auguste Viktoria wurden oder werden zeitnah (2021) eingestellt, die betreffenden Schächte verfüllt und mit Hüllrohren zu potentiellen Brunnenwasserhaltungen umgebaut.
Nach einer Anstauphase von mehreren Jahren sollen alle Grubenwässer der stillgelegten Wasserprovinzen in die Wasserprovinz Zollverein/Emschermulde übertreten³.
Ab 2026 soll das Niveau in der Provinz Zollverein/Emschermulde auf -726 mNN angestiegen sein und das Wasser dann im Bereich der ehem. Zeche Möller-Rheinbaben unter Bottrop in das Grubengebäude der Zeche Prosper-Haniel übertreten.
Von dort würde das es dann über den Schacht Hünxe zur 5. Sohle des Bergwerks Lohberg in Dinslaken fließen und in den Rhein abgepumpt werden.
Faktisch würde es also im zentralen Ruhrgebiet dann nur noch eine Wasserprovinz geben (Lohberg).
Das aus nicht verfüllten Abbaubereichen, Strecken, Schächten, Poren und Klüften bestehende Restholraumvolumen allein in dieser Provinz wird auf über 500 Mio. m³ geschätzt was dem einhundertneunzigfachen Volumen der Cheops-Pyramide entspricht.
Die Wassergängigkeit zwischen den verschiedenen Wasserprovinzen soll durch (z.T. neu aufgefahrene) Strecken, Bohrlöcher oder ehem. Abbauannäherungen der Zechen gewährleistet sein.
Problematisch erscheint die Übertrittsstelle Emschermulde-Haniel. Hier würde das gesamte Grubenwasser der stillgelegten Wasserprovinzen um Zollverein in die Provinz Haniel übertreten (circa 22 Mio. m³/J).
Mit einer 2200 m langen Erkundungsstrecke (letzte Streckenauffahrung im dt. Steinkohlenbergbau) ist daher 2015 von der Schachtanlage Haniel 2 aus dieser Bereich angefahren worden. Dabei wurde festgestellt, daß die aus den 1950er Jahren stammende, als Übertrittsstelle vorgesehene, ehem. Richtstrecke der Zeche Möller-Rheinbaben verbrochen ist.
Ob eine Ableitung der Grubenwässer nach Westen über die neue Erkundungsstrecke/Grubenwasserkanal in Gänze möglich seien wird ist also offen.
Bei einem teilweisen Versagen der Wasserwegigkeit sollen daher ab 2030 über den Schacht Zollverein 12 wieder bis zu 5,8 Mio. m³ pro Jahr gehoben werden.
Dafür belässt man in der anstehenden Schachtverfüllung zwei Hüllrohre zum Einbringen von Tauchpumpen. Das abgepumpte Grubenwasser soll anschließend übertägig zum ehem. Förderberg der Schachtanlage Prosper-Haniel fließen. Dazu würden bis zum RH-Kanal die vorhandenen Grubenwasserleitungen genutzt. Vom Bereich Schurenbachhalde bis zur Schachtanlage Prosper-Haniel würde eine neue Rohrtrasse entlang des RH-Kanals notwendig.
Um das Zollvereingrubenwasser durch den 3700 m langen Förderberg (davon 1170 m verfüllt) wieder nach Untertage einleiten zu können wurden dort kürzlich zwei Stränge aus insgesamt 2860 Betonröhren eingebaut.
Bei -626 mNN würde dieses Wasser dann dem Grubenwasserstrom Richtung Lohberg zugeführt und dort zum zweiten Mal gehoben.
Für den, unwahrscheinlichen, Fall eines Totalversagens der Überleitung im Grubenfeld Möller-Rheinbaben müßte auch der Schacht Zollverein 2 mit Tauchpumpen ausgestattet werden und zur Wasserhebung herangezogen werden. Da sich wg. schädlicher Ausfällungen die bariumhaltigen Grubenwässer aus der Wasserprovinz Zollverein-Emschermulde nicht mit den sulfathaltigen aus der Provinz Zollverein-Süd mischen sollen wird auf der 14. Zollvereinsohle ein Damm mit einem regelbaren Durchlass eingebaut der die Grubenwässer im Bedarfsfall trennen könnte.
Abgesehen von der hier beschriebenen Wasserhaltung im zentralen Ruhrgebiet wird es weiterhin die Wasserhaltungen Haus Aden (Einleitung Lippe), Robert Müser, Friedlicher Nachbar, Heinrich (Einleitung Ruhr) und Walsum (Einleitung Rhein) geben.
Die Grubenwässer aus der Wasserhaltung Concordia in Oberhausen werden zukünftig in die Wasserprovinz Walsum übertreten und dort abgepumpt.
Fernziel ist es alle Wasserhaltungen auf Brunnenbetrieb umzustellen auch um zukünftig kein Personal für den Untertagebetrieb mehr vorhalten zu müssen (z.B. Grubenwehr).
Das heißt natürlich auch, daß es in Kürze keinen Zugang zum ehem. Steinkohlentiefbau des Ruhrgebiets mehr geben wird.
Wer sich gerne näher mit dem Thema Grubenwasserkonzept befassen möchte:
Machbarkeitsstudie 1
Machbarkeitsstudie 2
Einleitung Förderberg Prosper
1 Grubenfelder: Zollverein V/VI, Zollverein-SW, Dahlbusch/Holland, Bonifacius, Katharina, Kg. Elisabeth, Vict. Mathias.
2 Grubenfelder: Zollverein III, Emil-Fritz, Prosper alt, Möller-Rheinbaben, Math. Stinnes, Wilh. Victoria, Nordstern, Graf Moltke, Hugo, Bismarck, Ewald, Schlägel & Eisen, Pluto, Consolidation, Recklinghausen, Blumenthal, König Ludwig, Ewald Fort., An der Haard, Emscher Lippe, Waltrop.
3 Carolinenglück (2022), Amalie (2022), AV > 2030.
Beitz-Villa abgerissen.
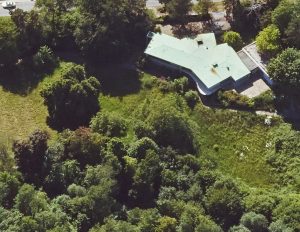
© RVR, 2020, dl-de/by-2-0
Bei einer freitäglichen Coronawanderung habe ich gesehen, daß die 1953 von der Fried. Krupp AG für ihren Generalbevollmächtigten Berthold Beitz erbaute Villa in Essen-Bredeney Geschichte ist.
Das KST-Desaster
Versuche ihre binnenländischen Hüttenwerke (Haspe, Georgsmarienhütte, und später auch die Maxhütte) vom teuren Hochofenbetrieb unabhängig zu machen und gleichzeitig eine Alternative zu der energieintensiven Stahlerzeugung im Siemens-Martinofen zu finden gab es bei der Klöckner-Werke AG schon Mitte der 1960er Jahre.
Im SM-Stahlwerk der Hasper Hütte wurde 1965 ein 60 t Versuchsofen mit Öl/O²-Brenner (zunächst über dann unter der Schmelze positioniert) in Betrieb genommen.
Nach der Stilllegung der Metallurgie in Haspe gingen die Versuche in Georgsmarienhütte weiter.
Dort wurde 1973 in einem mit seitlichen Öl/O²-Brennern ausgestattetem Ofen Schrott geschmolzen und direkt einem 20 t Elektrolichtbogenofen zur Stahlerzeugung zugeführt.
Dieses Verfahren wurde Klöckner-Stahlerzeugung-Elektrolichtbogenofen (KSE) genannt.
Die Versuche waren äußerst viel versprechend mit der 2. Ölkriese wurden 1979 Öl und Erdgas aber so teuer, daß man sich nach einem neuen Verfahren umschauen mußte.
Gegen den Widerstand der GMH-Werksleitung, die einen Elektrolichtbogenofen präferierte, wurde durch die Duisburger Konzernzentrale mit dem Technikvorstand Ludwig v. Bogdandy ein bis dahin (bis auf wenige Vorversuche in der Maxhütte) völlig unbekanntes Verfahren realisiert, das Klöckner-Stahl-Tiegel-Stahlwerk (KST).
Dort sollte möglichst ohne Flüssigeinsatz aus Schrott durch einblasen von billiger Feinkohle (oder Feinkoks), Sauerstoff und Erdgas durch den Boden eines 125 t Konverters Stahl erzeugt werden.
Die 170 Mio. DM Investition ging im November 1981 in Betrieb.
Im ersten Betriebsjahr kam es gleich zu massiven Störungen, so dass die riesige Anlage nur zu 65 % ausgelastet werden konnte. Ein Betrieb ohne Flüssigroheisen vom Hochofen 3 erwies sich daher als unmöglich.
1983, bei sinkenden Schrottpreisen, kam es zu einem zweiten Versuch den neuen Konverter nur mit Feststoffen zu beschicken. Der Betrieb wurde auf das Partielle-Schmelzen-Rückführungsverfahren (PSR) umgestellt.
Dabei wurde in zwei Schritten synthetisches Roheisen im Konverter erzeugt, entnommen, zwischengelagert und der nächsten Schmelze wieder zugeführt.
Nun glaubte man eine dauerhafte Lösung für das KST-Stahlwerk gefunden zu haben. Der Hochofen 3 wurde am 27.4.1983 ausgeblasen und sollte auf Wunsch der Konzernleitung sofort abgerissen werden was aber nicht geschah.
Steigende Schrottpreise und die hohen Betriebskosten des komplizierten Verfahrens führten schon 1984 zu einer Rückkehr zum Flüssigeinsatz im Konverter, der Hochofen wurde wieder angeblasen.
Dabei blieb es bis zur Inbetriebnahme des neuen Gleichstrom-Lichtbogenofens in 1994. KS-Stahlwerk und Hochofen 3 wurden endgültig stillgelegt und abgerissen.
Das KST-Verfahren hat den Stahlstandort Georgsmarienhütte an den Rand des Abgrunds geführt, zeigt aber auch wie innovativ und risikofreudig ein Teil der deutschen Stahlindustrie auf die große Krise der 1970er Jahre reagierte.
Stahlstadt Essen
Der Mythos der Stahlstadt Essen hat Dank der Fried. Krupp AG den 2. Weltkrieg überdauert.
Man sprach immer noch von der Essener Gußstahlfabrik.
Tatsächlich gab es aber nach 1945 keine nennenswerte Stahlproduktion mehr in der Stadt.
Vor dem Krieg (1936) hatte Krupp in Essen noch 261.000 t Roheisen und 625.000 t Rohstahl produziert. Nach der Stilllegung und Demontage des Hochofenwerks in Borbeck und der drei Siemens-Martin Stahlwerke produzierte Krupp 1960 nur noch in jeweils einem Lichtbogenofen und einem Kupolofen (24) Stahl und Eisen für den Eigenbedarf der Schmiede (13) und der Eisengießerei (24). Ansonsten handelte es sich bei Krupp in Essen nun um ein Sammelsurium aus Leichtmachinen-, Schwermaschinen- und Anlagenbau, Fahrzeugbau und Dienstleistern.
1960 wurden auch große Bereiche der ehem. Gußstahlfabrik durch Fremdfirmen genutzt oder waren verkauft worden (z.B. die Landmaschinenfertigung an der Hans-Böcklerstr.).
Das Luftbild zeigt den Zustand in den frühen 1960er Jahren.
Die Massenstahlerzeugung war zu diesem Zeitpunkt schon nach Rheinhausen und zum neu erworbenen Bochumer Verein verlagert worden.
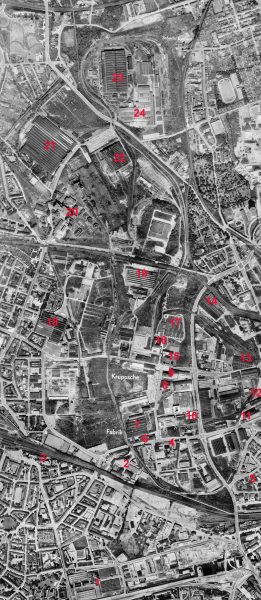
© RVR, 1969, dl-de/by-2-0
1 Widia
2 Baubetriebe
3 Bürohaus Westbahnhof
4 Lagerhaus Chemiebau
5 Unfallambulanz
6 Grafische Anstalt
7 Mechanische Werkstatt, Labor
8 Gas- und Wasserwerke
9 Eisen u. Stahlhandel, Krupp-Indien Handelsgesellschaft
10 Sauerstoff- Wasserstoff- Druckluftversorgung, Zurichterei
11 Essener Schweißelektrodenwerk
12 Krupp Dolberg
13 Press- und Hammerwerk
14 Krupp Ardelt
15 Konzernleitung, Turmhaus
16 Bürogebäude 2
17 Lehrwerkstatt
18 Motoren- und Kraftwagenfabriken
19 Motoren- und Kraftwagenfabriken
20 Bergwerk Helene-Amalie
21 Leichtmaschinenbau, Apparatebau
22 Pressenbau, Getriebebau
23 Lokomotivbau, Dieselmotorenbau
24 Gießerei, LD-Versuchsstahlwerk
Where two passions meet.
The legendary US underground band Pere Ubu from Cleveland, Ohio was one of the first to address the atmosphere of their declining heavy industrial homeland in lyrics and on record covers.
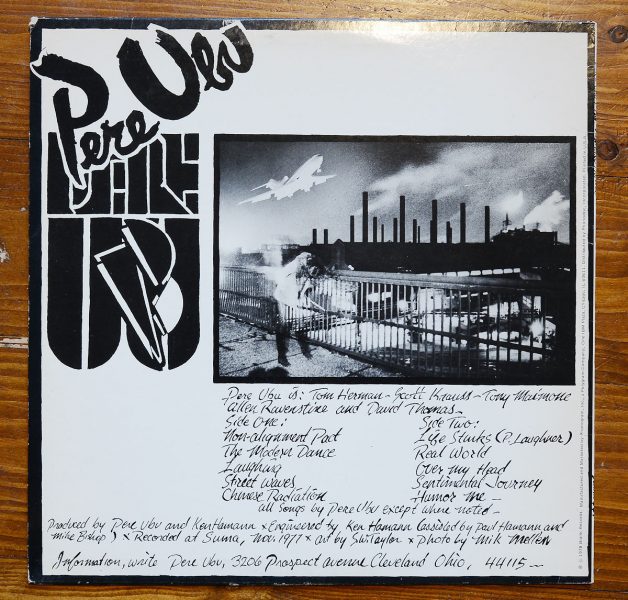
From now demolished Pershing Av. bridge.
No. 1 slabbing mill in the foreground, no. 2 BOF right, open hearth shop in the background.
Frontman and mastermind David Thomas on growing up in Cleveland in the 1970ies:
We were savages living in the ruins of a great civilization of Rockefellers and Carnegies. Growing up, we owned downtown. Nobody wanted it. We roamed the streets like they were ours. The Flats was a place of deep mystery. It was our modern art museum. We would drive through the steel mills and within 20 yards of open blast furnaces. We weren’t duplicating those sounds. Those sounds were showing us the way to change the narrative vehicle of modern music.
(Cleveland Magazine, 11/22/2017)
Can anyone raise the bid ?
16, according to my estimation this is the largest number of blast furnaces in a steel plant that currently exists. And that probably applies to the past as well.
US Steel’s Gary works in it’s heydays never had more than 12, Sparrows Point 10. Reichswerke in Salzgitter, Germany had 32 planned but only 12 were completed.
Rizhao Steel in China (Shandong Province) was founded in 2003. After only 181 days of construction, the first blast furnace was blown in September 2003. By 2008, 15 additional furnaces had been built (cap 7.5 mio t/y).
The small size of the blast furnaces (2 x 450 m³, 2 x 530 m³, 2 x 580 m³, 10 x 1080 m³) is striking. This would have made the plant uncompetitive in Western Europe and especially in North America already in the 1960s.
The installation of such small furnaces was widespread in China (presumably due to poor coke quality and a lack of know-how) until the economic crisis of 2008.
For economical and ecological reasons, however, the days of such blast furnaces are probably numbered in China as well.
Rizhao steel is building three new blast furnaces right now 3000 m³ volume each.
Grobblechstraße stillgelegt.
Mit der gestrigen Mittagsschicht hat thyssenkrupp Steel die Produktion von Grobblechen eingestellt.
Das Grobblechwalzwerk in Duisburg-Hüttenheim wurde 1963 durch die Mannesmann AG zur Versorgung des benachbarten Großrohrwerks (Stilllegung 1978) mit Blechen erbaut.
1970 übernahm die August Thyssen Hütte im Tausch mit ihren Rohrwerken die Flachstahlsparte von Mannesmann. 1978 wurde das neue 3,9 Meter Quartogerüst durch die Sack Maschinenbau GmbH installiert.
Die Hüstener Gewerkschaft
In die Abteilung vergessener Hüttenwerke gehört das Werk in Hüsten (heute zu Arnsberg) direkt an der Ruhr.
Das Hochofenwerk wurde 1908/9 erbaut und schon 1927 wieder stillgelegt und abgerissen.
Zur Hütte gehörte auch ein Siemens-Martin Stahlwerk mit vier Öfen (3x 15 t, 1 x 30 t), und eine Kokerei.
In den 1930er Jahren wurde in Hüsten noch ein Warmbandwalzwerk gebaut.
Diese Anlage kam nach dem 2 . Weltkrieg dann zur Hüttenwerke Siegerland AG und wurde 1966, nach der Übernahme durch die Hoesch AG, stillgelegt.
Das Hüttenwerksgelände wird heute durch ein Gewerbegebiet neu genutzt.
Three days over Shanxi
One of the few things I would really miss without internet are the aerial photos from various sources that can be used nowadays quite conveniently. Since 2009 (Vs. 5) Google Earth Pro offers the possibility to load historical aerial images. Although the quality of the images varies greatly and only recent history is covered, they are often very helpful. So I recently went on a flight over Shanxi, China’s largest coalfield. Shanxi, not to be confused with the adjoining Shaanxi province to the west, is about twice the size of Bavaria. Coal mining takes place in practically all parts of the province. From large open pits in the northwest to countless drift mines and deep mines.Despite the Corona winter I quickly buried the plan to mark all the mines I saw, because there are too many, and anyway it’s only mining, not my core business. So I focussed on coking plants. Shanxi is Chinas largest coke producer so I thought there must be some.
I found 260 on the aerial photos taken between 2008 and 2013 (there were still five coking plants in Germany in 2008), and these are only the larger plants, the traditional beehive ovens, which must have still existed at that time, despite the ban, are barely visible on aerial photos.
That China has made enormous efforts in the last 10 years to get its environmental problems under control which is evident from the fact that 146 of the approximately 260 coking plants that were still visible in Shanxi in 2008 have by now been shut down. With it’s remaining 114 plants (and I’m sure I’ve overlooked a few), Shanxi produces 20 % of China’s coke (2019), which in turn accounts for 60 % of the world’s production.
As in many communist economies, the core aggregates of the heavy industry are often standardized in China.
Very typical, for example, are stamp charged coking plants (relatively easy to recognize by the coal tower standing next to the batteries) with two batteries and 4.3 meter furnaces. In these plants, even low-grade coals can be processed into usable blast furnace coke by precompression.
But there are ultra modern facilities too like the one in Xiangfen (65). The only coke plant I have ever seen with dust removal sheds on both the coke and pusher sides of the batteries
About half of the coking plants in Shanxi were top loaders (and apparently there were also combined plants) of older or newer design. 25 plants used non recovery ovens in which no by-products are produced.
Very few Chinese coking plants are attached to coal mines (as was common in Germany), some are operated by the larger steel mills, but by far the majority are stand-alone operations.
What is really remarkable is the fact that most of the coking plants do not have a rail connection. The entire supply and disposal of coal, coke and by-products at these plants is handled by trucks.
If you are interested you can download the KMZ file for Google Earth with the coking plant locations in Shanxi here: Shanxi Coking Plants.KMZ
In case this program is not familiar: You can import the KMZ file directly (under File), the historical aerial photos can then be found under the 7th icon from the left in the menu bar (clock symbol).
Decommissioned coking plants have a red icon. Sometimes it was not quite clear whether the plant was already closed down, but if the pusher cars hadn’t changed position for years and the coal yard was empty I assumed that the place was dead.
Since most of the plants in Shanxi disappear quickly after they are shut down, the region is not very productive for the Urbex scene (is there one in China ?).However, some plants seem to be preserved (e.g. 212,211,128,136,194,235). Two stand apparently unfinished as malinvestments (251,252).
If you find any other coking plants please let me know, but beware those aerials can be a bit addictive.