50 years ago the Rheinstahl AG from Essen, Germany finally cancelled it’s plans to built a BOF shop, a continuous caster and a bar rolling mill at it’s foundry site in Gelsenkirchen.
The Schalker Gruben- und Hüttenverein was founded in 1872 and became Europe’s largest iron foundry after the second world war, employing more than 6000 people. The plans provided an investment of more than 300 Mio.German Marks and an initial capacity of 600.000 tons of steel per year. Though the ground (north of the foundry no.3, next to the Wannerstrasse) was already prepared the whole project was called off due to growing overcapacities on the steel market. So the Schalker Verein stayed an iron foundry with four blast furnaces, a pipe casting mill, two fittings-foundries and a foundry for large castings up to 40 tons a piece
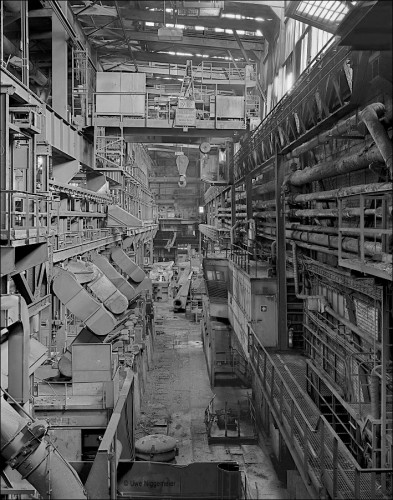
The image shows the melt shop of the pipe casting mill where ductile iron pipes with a diameter up to 1,4 meter were casted. The shop included a 160 ton hot metal mixer and five 13 ton induction furnaces and was built in 1966. The hot metal was provided by the Schalker Verein blast furnaces and later came from Thyssen’s Duisburg Meiderich site (today: Landschaftspark Nord).
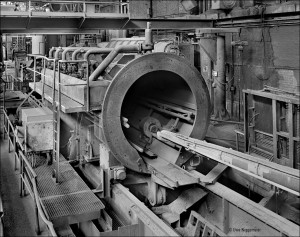
The foundry was sold to Thyssen in 1973.The last blast furnace was closed in 1982. The three remaining blast furnaces were demolished in-between April and September of 1983.
The last pipe was casted in 2004 (meanwhile the mill was sold to the French Pont a Mousson/Saint Gobain company). Most of the ground is a redevelopment site by now.
Some historic images at Daniel Hinze’s site.
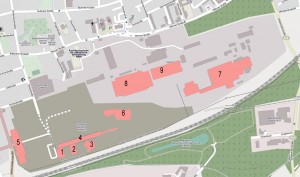
1: Blast furnace no.1 (Hochofen 1)
2: Blast furnace no.2 (Hochofen 2)
3: Blast furnace no.4 (Hochofen 4)
4: Storage with highline (Möllerbunker)
5: Power station (Kraftzentrale)
6: Sinter plant (Sinteranlage)
7: Pipe foundry (Rohrgiesserei)
8: Fittings foundry no.1 ( Formstückgiesserei 1)
9: Foundry for large castings (Grossgusswerk)